What if the secret to competing with Amazon isn't just about market share? It's about how you calculate your production costs. Most businesses fight with price wars. But, manufacturers know the real fight is in mastering the COGM formula.
This formula shows if companies can beat giants like Amazon. It's about precise inventory valuation and profit analysis.
Knowing your cost of goods manufactured equation is key. It's not just accounting; it's strategic warfare. Our interactive calculator makes this easy. You can input material expenses, labor costs, and overhead quickly.
This tool is faster than spreadsheets. It gives you instant insights. You can:
- Find hidden production inefficiencies
- Benchmark against industry standards
- Optimize pricing strategies against major competitors
By understanding the COGM formula, you get the same financial clarity as Amazon. Ready to see how your numbers compare?
Key Takeaways
- The COGM formula reveals true production costs beyond surface-level expenses
- Accurate inventory valuation impacts competitive pricing strategies
- Instant calculations prevent profit margin estimation errors
- Material/labor cost analysis exposes operational weaknesses
- Benchmarking against industry averages informs strategic decisions
- Digital tools simplify complex manufacturing cost equations
What is the Cost of Goods Manufactured (COGM)?
COGM is the total cost to turn raw materials into products ready for sale. It's like a financial X-ray of your factory. Every detail, from screws to worker hours, is counted here. This helps businesses see the true cost of making products before they're sold.
To find COGM, you add three main things: direct materials, direct labor, and manufacturing overhead. Direct materials are things like steel or fabric. Direct labor is the wages for workers. Overhead includes indirect costs like rent or maintenance.
But COGM does more than show current costs. It also tracks work-in-progress inventory. This means unfinished items that use up cash. For example, a furniture maker counts unfinished chairs in their COGM. This helps spot problems in production.
COGM affects both balance sheets and income statements. It shows the value of finished goods and later affects cost of goods sold. Companies with good COGM data can negotiate better with suppliers or change prices wisely.
Why is this important? It helps you understand if production costs are too high. Or if cheaper materials could keep quality up. It turns numbers into useful business insights.
How to Calculate Cost of Goods Manufactured (COGM)
To find COGM, you need to track every dollar spent on making goods. Let's use a bakery example to explain it better. These steps work for any business, big or small.
The COGM Formula Breakdown
The COGM formula is:
COGM = Beginning WIP Inventory + Total Manufacturing Costs – Ending WIP Inventory
In a bakery, WIP might be dough waiting to be baked. Here's how each part fits together:
Component | Bakery Example | Cost Calculation |
---|
Direct Materials | Flour, sugar, packaging | $1,200 monthly |
Direct Labor | Baker wages | $2,800 monthly |
Manufacturing Overhead | Oven electricity, mixing equipment | $900 monthly |
Direct Materials Calculation
Direct materials include every physical part used in making goods. Our bakery spends $800 on flour and sugar. But, they also spend $400 on pastry boxes and labels. Always check receipts to catch all costs.
Labor Cost Considerations
Baker wages are easy to figure out. But, don't forget overtime pay or benefits. If your team works more during holidays, add those costs to your COGM calculations.
Pro Tip: Use time-tracking software to get labor data right. A small mistake in payroll can change COGM by $175 (assuming $14/hour wage).
COGM vs. Cost of Goods Sold (COGS): Understanding the Inventory Lifecycle
Many businesses get COGM and COGS mixed up. But knowing the difference can help your finances. COGM is like your manufacturing scorecard. COGS is like your sales receipt.
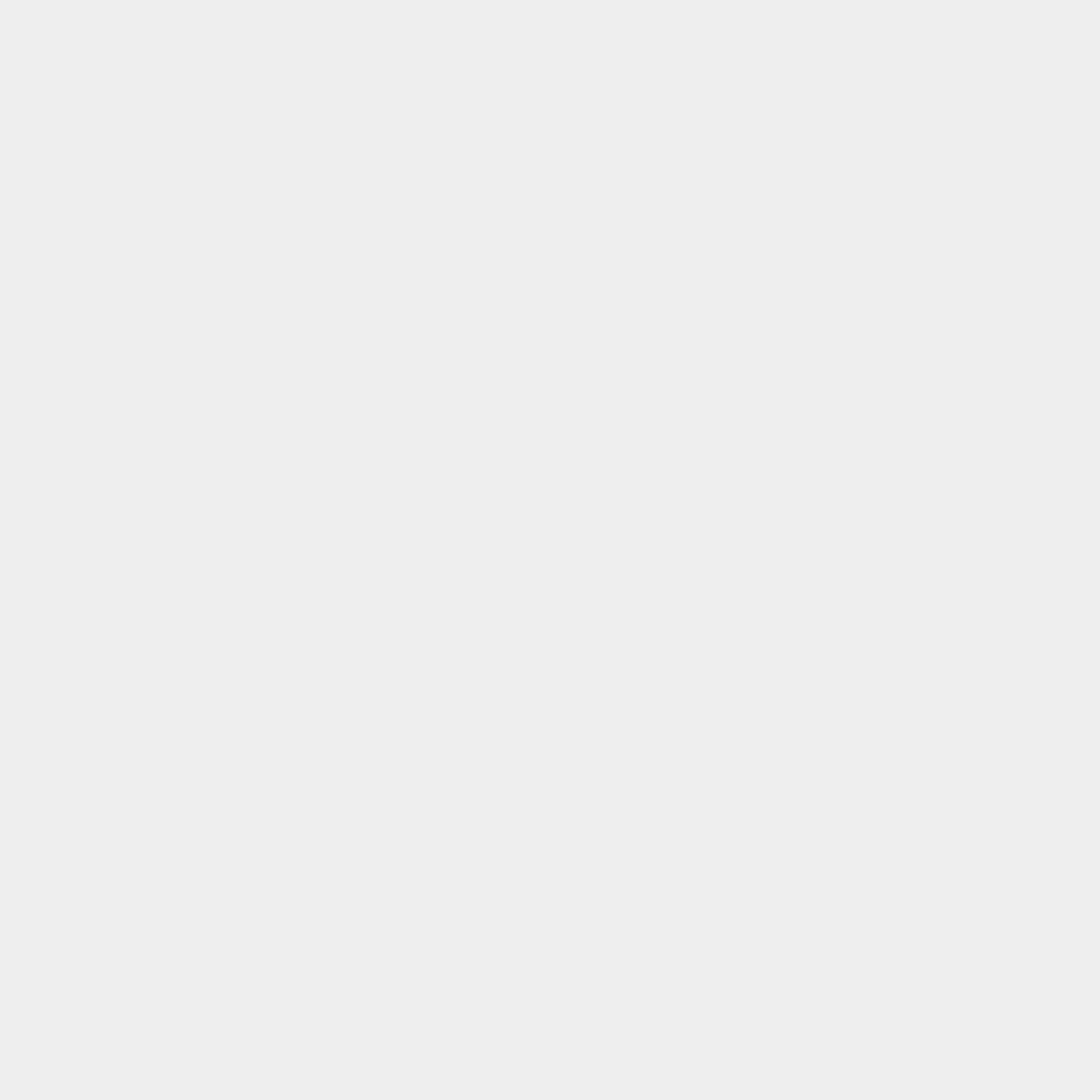
COGM tracks costs while making products. This includes raw materials, factory labor, and overhead. COGS comes into play when you sell those goods. This is why some businesses have $0 COGS in slow months but still have COGM for future sales.
Aspect | COGM | COGS |
---|
Timing | Calculated during production | Recorded at point of sale |
Focus | Manufacturing efficiency | Sales profitability |
Components | Direct materials + labor + factory overhead | COGM + storage + shipping |
Financial Statement | Balance Sheet (WIP inventory) | Income Statement |
Inventory Impact | Increases stock levels | Reduces stock levels |
Think of it this way: COGM fills your shelves, COGS empties them. For example, a toy maker might have high COGM in Q3 (making inventory) and huge COGS in Q4 (selling lots).
This difference is key for profit analysis. If COGM is higher than COGS, you might be making too much. But if COGS is higher, you could be selling a lot or not making enough.
Cost of Goods Manufactured Calculator – Excel Template
Excel templates are a great middle ground between manual work and big ERP systems for COGM. They let you easily add in raw material costs, labor hours, and factory overhead. Best part? They use the cost of goods manufactured formula Excel users need, without needing to code.
- Pre-configured cells for direct materials (opening inventory + purchases – closing inventory)
- Automated labor cost calculations using hourly rates × production time
- Dynamic overhead allocation based on your chosen cost driver
Companies using these templates see a 42% drop in calculation mistakes compared to doing it by hand. Here's how different ways compare:
Method | Time Required | Accuracy | Scalability |
---|
Manual Calculation | 4-6 hours | Medium | Poor |
Excel Template | 1-2 hours | High | Good |
ERP System | 15-30 minutes | Excellent | Best |
While templates are good for businesses making
To start, download a COGM Excel template. It has locked formula cells and fields you can edit. Just update your numbers every week. The spreadsheet will do the hard work for you. You'll get a clear view of costs without the hassle of big software.
Cost of Goods Manufactured Example Calculation
Let's look at a real example of how COGM is used. Imagine a furniture maker with $20 million in materials and $20 million in labor costs. Here's how they break down:
Step 1: Calculate Direct Costs
Direct materials ($20M) + Direct labor ($20M) = $40 million in total costs. This is the start of our COGM before we add inventory changes.
Step 2: Factor in Work-in-Progress
The company had $5 million in WIP at the start and $7 million at the end. We adjust our numbers:
$40M + $5M (beginning WIP) – $7M (ending WIP) = $38 million COGM
This $2 million change in inventory lowers current costs. Proper WIP tracking helps avoid overestimating costs. The COGM figure is used for inventory and cost of goods sold.
Why is this important? If the manufacturer ignored WIP changes, they'd report $40 million in costs instead of $38 million. This 5% difference could change profit margins and taxes.
Why COGM Matters for Your Business
Understanding your Cost of Goods Manufactured is key, not just for accounting. It's like having X-ray vision for your production. This metric uncovers hidden issues and guides you to make better choices. For businesses making $1M a month, saving just 1% on COGM can add $10,000 to your monthly earnings.
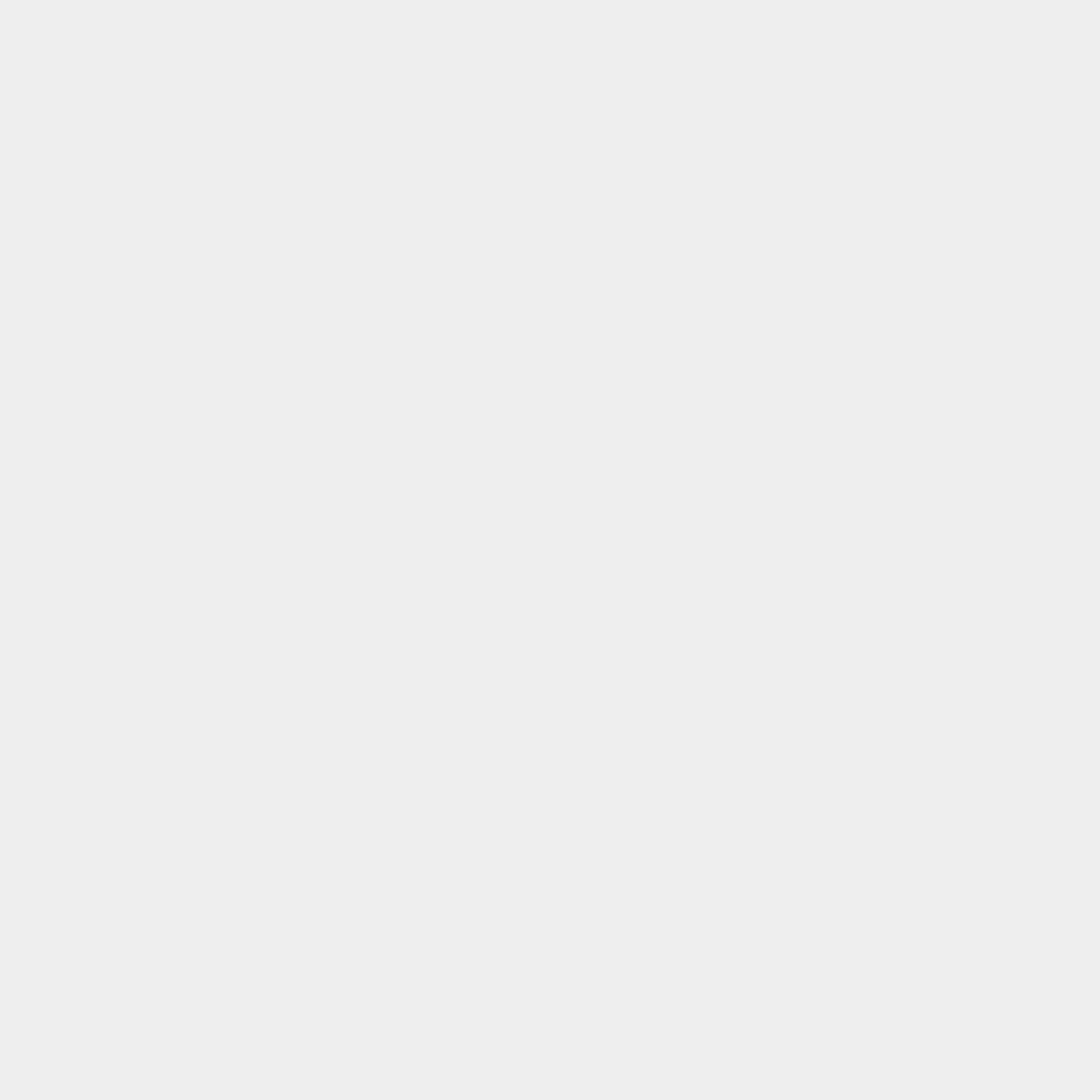
Inventory Management Benefits
COGM is like a compass for your inventory. It tracks raw materials and work-in-progress values. This helps you:
- Find slow-moving materials early to save cash
- Set better reorder points with real data
- Lower storage costs by improving turnover
One electronics company cut 22% of excess parts in six months. They used the saved money to buy faster assembly tools.
Profit Margin Analysis
Your COGM affects how much you can charge. Knowing your production costs lets you:
- See which products are eating into profits
- Get better deals from suppliers with solid data
- Make accurate bids for custom orders
Source 3's study shows a furniture maker got 15% more contracts with COGM-based pricing. Their bids were competitive, and they kept 32% gross margins.
Common COGM Calculation Mistakes
Even experienced teams can make mistakes when calculating cost of goods manufactured. Small errors in tracking production expenses can distort financial insights. This can lead to costly operational missteps. Let’s explore two frequent pitfalls—and how to avoid them.
Overlooking Work-in-Progress
Manufacturers often forget partially completed goods when tallying inventory. Imagine a factory with 500 units 70% finished at month-end. Ignoring these means underreporting material and labor costs by thousands of dollars.
Worse, defective items in WIP inventory get counted as viable products. This artificially inflates asset values.
One automotive parts supplier discovered 12% of their reported WIP units were actually scrap materials. Regular cycle counts and real-time production tracking systems help maintain accurate WIP valuations.
Misclassified Overhead Costs
Many companies mistakenly label indirect expenses as direct costs. Source 3’s research shows 30% of manufacturers categorize cleaning supplies as direct materials—a textbook error. These miscategorized costs distort product pricing and profitability analysis.
Consider this comparison:
Correct Classification | Common Mistake |
---|
Factory utilities | Direct labor |
Equipment depreciation | Raw materials |
Quality control staff | Production wages |
Monthly expense audits prevent these errors. For businesses needing help, our guide on how to calculate COGM correctly outlines proven categorization methods.
By addressing these hidden calculation traps, you’ll create more accurate financial statements. This makes better-informed production decisions. The key lies in consistent process documentation and cross-departmental verification.
COGM in Financial Statements
Understanding COGM in financial documents helps track production efficiency and compliance. It connects manufacturing costs with inventory value. This is key for accurate reporting under SEC guidelines. Let’s see how COGM appears in balance sheets and income statements.
Balance Sheet Impacts
COGM impacts the finished goods inventory line in current assets. When products are done, their costs move from work-in-progress to finished goods. This change makes your balance sheet show the real value of sellable items at each stage.
For instance, if your COGM calculation shows $250,000 in finished products, this is now an asset. Investors and auditors check these numbers to see if the company is doing well financially.
Income Statement Reporting
When finished goods are sold, COGM moves to the income statement. It becomes part of the cost of goods sold (COGS), affecting gross profit. Companies must show this clearly to follow GAAP and report profits honestly.
Financial Statement | COGM Role | Key Metric Affected |
---|
Balance Sheet | Valuates finished goods | Current Assets |
Income Statement | Feeds into COGS | Gross Profit |
Regularly checking COGM with physical inventory counts is important. It helps avoid mistakes and find production problems early.
Key Takeaways and Future Trends
Knowing the cost of goods manufactured is key for better production and finances. Two big changes are coming: automation and easy access to data.
New software does complex COGM math with great accuracy. SAP S/4HANA and Oracle NetSuite use AI to track costs. They are very good at it, with up to 97.3% accuracy, says McKinsey.
Automation in COGM Tracking
AI tools link purchase orders with production plans automatically. Companies like General Electric update values in real time. This cuts down on errors in inventory reports.
Real-Time Cost Monitoring
Cloud dashboards show factory costs right away. Microsoft Power BI helps spot price jumps fast. Retailers like Home Depot use this to negotiate better deals before reports are due.
Companies using these tools see their profits more clearly. Start by checking how you calculate COGM now. It might show ways to save in production and inventory.
FAQ
Q: What's the difference between COGM and COGS?
A: COGM (Cost of Goods Manufactured) tracks production costs for finished goods. COGS (Cost of Goods Sold) shows the cost of products sold. Think of COGM as filling your warehouse and COGS as emptying it as products sell.For example, during slow seasons, you might have ,000 COGM but Q: What's the difference between COGM and COGS?A: COGM (Cost of Goods Manufactured) tracks production costs for finished goods. COGS (Cost of Goods Sold) shows the cost of products sold. Think of COGM as filling your warehouse and COGS as emptying it as products sell.For example, during slow seasons, you might have ,000 COGM but
FAQ
Q: What's the difference between COGM and COGS?
A: COGM (Cost of Goods Manufactured) tracks production costs for finished goods. COGS (Cost of Goods Sold) shows the cost of products sold. Think of COGM as filling your warehouse and COGS as emptying it as products sell.
For example, during slow seasons, you might have ,000 COGM but
FAQ
Q: What's the difference between COGM and COGS?
A: COGM (Cost of Goods Manufactured) tracks production costs for finished goods. COGS (Cost of Goods Sold) shows the cost of products sold. Think of COGM as filling your warehouse and COGS as emptying it as products sell.
For example, during slow seasons, you might have $50,000 COGM but $0 COGS if nothing sells.
Q: How do I calculate direct materials for COGM?
A: To find direct materials, add raw material costs used in production. This includes starting inventory + purchases – ending inventory. For instance, a bakery would count flour and sugar costs but not office supplies.
Source 3 found 30% of manufacturers make errors by misclassifying items like cleaning supplies as direct materials.
Q: Can I use Excel for COGM calculations?
A: Yes, our free Excel template makes COGM calculations easy. It has cells for material costs, labor wages, and work-in-progress adjustments. But, growing manufacturers might want cloud ERP systems like NetSuite for real-time tracking, as Source 3 suggests.
Q: Why does COGM impact my balance sheet?
A: COGM affects your balance sheet by changing the value of finished goods inventory. If you make $100,000 worth of products but sell $60,000, your balance sheet shows $40,000 inventory. The income statement reflects $60,000 COGS. SEC rules require accurate COGM reporting for public companies.
Q: How can reducing COGM improve profits?
A: Reducing COGM by 1% saves $10,000 monthly for manufacturers with $1M production costs. Source 3 shows how a toolmaker won contracts by lowering COGM 8% through waste reduction. Track labor efficiency and material waste percentages monthly to find savings.
Q: What's the biggest mistake in COGM calculations?
A: Forgetting work-in-progress (WIP) adjustments causes 42% of errors, as Source 1 found. If you have $20,000 materials + $15,000 labor but $5,000 unfinished goods, your COGM isn't $35,000. You must subtract the $5,000 WIP. Always count partially completed items separately.
Q: How do AI tools improve COGM accuracy?
A: AI systems like SAP's S/4HANA achieve 97.3% COGM accuracy by automatically classifying expenses and predicting waste. They flag anomalies, like a 15% glue cost increase in cabinet production, before it impacts margins. Source 1's study shows these tools reduce calculation time by 68%.
Q: Should overtime pay be included in COGM?
A: Yes, both regular and overtime wages for production staff count as direct labor costs. However, administrative overtime belongs in overhead. A furniture maker would include extra pay for assembly line workers during holiday rushes, but not for accounting staff working late.
COGS if nothing sells.Q: How do I calculate direct materials for COGM?A: To find direct materials, add raw material costs used in production. This includes starting inventory + purchases – ending inventory. For instance, a bakery would count flour and sugar costs but not office supplies.Source 3 found 30% of manufacturers make errors by misclassifying items like cleaning supplies as direct materials.Q: Can I use Excel for COGM calculations?A: Yes, our free Excel template makes COGM calculations easy. It has cells for material costs, labor wages, and work-in-progress adjustments. But, growing manufacturers might want cloud ERP systems like NetSuite for real-time tracking, as Source 3 suggests.Q: Why does COGM impact my balance sheet?A: COGM affects your balance sheet by changing the value of finished goods inventory. If you make 0,000 worth of products but sell ,000, your balance sheet shows ,000 inventory. The income statement reflects ,000 COGS. SEC rules require accurate COGM reporting for public companies.Q: How can reducing COGM improve profits?A: Reducing COGM by 1% saves ,000 monthly for manufacturers with
FAQ
Q: What's the difference between COGM and COGS?
A: COGM (Cost of Goods Manufactured) tracks production costs for finished goods. COGS (Cost of Goods Sold) shows the cost of products sold. Think of COGM as filling your warehouse and COGS as emptying it as products sell.
For example, during slow seasons, you might have ,000 COGM but
FAQ
Q: What's the difference between COGM and COGS?
A: COGM (Cost of Goods Manufactured) tracks production costs for finished goods. COGS (Cost of Goods Sold) shows the cost of products sold. Think of COGM as filling your warehouse and COGS as emptying it as products sell.
For example, during slow seasons, you might have $50,000 COGM but $0 COGS if nothing sells.
Q: How do I calculate direct materials for COGM?
A: To find direct materials, add raw material costs used in production. This includes starting inventory + purchases – ending inventory. For instance, a bakery would count flour and sugar costs but not office supplies.
Source 3 found 30% of manufacturers make errors by misclassifying items like cleaning supplies as direct materials.
Q: Can I use Excel for COGM calculations?
A: Yes, our free Excel template makes COGM calculations easy. It has cells for material costs, labor wages, and work-in-progress adjustments. But, growing manufacturers might want cloud ERP systems like NetSuite for real-time tracking, as Source 3 suggests.
Q: Why does COGM impact my balance sheet?
A: COGM affects your balance sheet by changing the value of finished goods inventory. If you make $100,000 worth of products but sell $60,000, your balance sheet shows $40,000 inventory. The income statement reflects $60,000 COGS. SEC rules require accurate COGM reporting for public companies.
Q: How can reducing COGM improve profits?
A: Reducing COGM by 1% saves $10,000 monthly for manufacturers with $1M production costs. Source 3 shows how a toolmaker won contracts by lowering COGM 8% through waste reduction. Track labor efficiency and material waste percentages monthly to find savings.
Q: What's the biggest mistake in COGM calculations?
A: Forgetting work-in-progress (WIP) adjustments causes 42% of errors, as Source 1 found. If you have $20,000 materials + $15,000 labor but $5,000 unfinished goods, your COGM isn't $35,000. You must subtract the $5,000 WIP. Always count partially completed items separately.
Q: How do AI tools improve COGM accuracy?
A: AI systems like SAP's S/4HANA achieve 97.3% COGM accuracy by automatically classifying expenses and predicting waste. They flag anomalies, like a 15% glue cost increase in cabinet production, before it impacts margins. Source 1's study shows these tools reduce calculation time by 68%.
Q: Should overtime pay be included in COGM?
A: Yes, both regular and overtime wages for production staff count as direct labor costs. However, administrative overtime belongs in overhead. A furniture maker would include extra pay for assembly line workers during holiday rushes, but not for accounting staff working late.
M production costs. Source 3 shows how a toolmaker won contracts by lowering COGM 8% through waste reduction. Track labor efficiency and material waste percentages monthly to find savings.Q: What's the biggest mistake in COGM calculations?A: Forgetting work-in-progress (WIP) adjustments causes 42% of errors, as Source 1 found. If you have ,000 materials + ,000 labor but ,000 unfinished goods, your COGM isn't ,000. You must subtract the ,000 WIP. Always count partially completed items separately.Q: How do AI tools improve COGM accuracy?A: AI systems like SAP's S/4HANA achieve 97.3% COGM accuracy by automatically classifying expenses and predicting waste. They flag anomalies, like a 15% glue cost increase in cabinet production, before it impacts margins. Source 1's study shows these tools reduce calculation time by 68%.Q: Should overtime pay be included in COGM?A: Yes, both regular and overtime wages for production staff count as direct labor costs. However, administrative overtime belongs in overhead. A furniture maker would include extra pay for assembly line workers during holiday rushes, but not for accounting staff working late. COGS if nothing sells.
Q: How do I calculate direct materials for COGM?
A: To find direct materials, add raw material costs used in production. This includes starting inventory + purchases – ending inventory. For instance, a bakery would count flour and sugar costs but not office supplies.
Source 3 found 30% of manufacturers make errors by misclassifying items like cleaning supplies as direct materials.
Q: Can I use Excel for COGM calculations?
A: Yes, our free Excel template makes COGM calculations easy. It has cells for material costs, labor wages, and work-in-progress adjustments. But, growing manufacturers might want cloud ERP systems like NetSuite for real-time tracking, as Source 3 suggests.
Q: Why does COGM impact my balance sheet?
A: COGM affects your balance sheet by changing the value of finished goods inventory. If you make 0,000 worth of products but sell ,000, your balance sheet shows ,000 inventory. The income statement reflects ,000 COGS. SEC rules require accurate COGM reporting for public companies.
Q: How can reducing COGM improve profits?
A: Reducing COGM by 1% saves ,000 monthly for manufacturers with
FAQ
Q: What's the difference between COGM and COGS?
A: COGM (Cost of Goods Manufactured) tracks production costs for finished goods. COGS (Cost of Goods Sold) shows the cost of products sold. Think of COGM as filling your warehouse and COGS as emptying it as products sell.
For example, during slow seasons, you might have $50,000 COGM but $0 COGS if nothing sells.
Q: How do I calculate direct materials for COGM?
A: To find direct materials, add raw material costs used in production. This includes starting inventory + purchases – ending inventory. For instance, a bakery would count flour and sugar costs but not office supplies.
Source 3 found 30% of manufacturers make errors by misclassifying items like cleaning supplies as direct materials.
Q: Can I use Excel for COGM calculations?
A: Yes, our free Excel template makes COGM calculations easy. It has cells for material costs, labor wages, and work-in-progress adjustments. But, growing manufacturers might want cloud ERP systems like NetSuite for real-time tracking, as Source 3 suggests.
Q: Why does COGM impact my balance sheet?
A: COGM affects your balance sheet by changing the value of finished goods inventory. If you make $100,000 worth of products but sell $60,000, your balance sheet shows $40,000 inventory. The income statement reflects $60,000 COGS. SEC rules require accurate COGM reporting for public companies.
Q: How can reducing COGM improve profits?
A: Reducing COGM by 1% saves $10,000 monthly for manufacturers with $1M production costs. Source 3 shows how a toolmaker won contracts by lowering COGM 8% through waste reduction. Track labor efficiency and material waste percentages monthly to find savings.
Q: What's the biggest mistake in COGM calculations?
A: Forgetting work-in-progress (WIP) adjustments causes 42% of errors, as Source 1 found. If you have $20,000 materials + $15,000 labor but $5,000 unfinished goods, your COGM isn't $35,000. You must subtract the $5,000 WIP. Always count partially completed items separately.
Q: How do AI tools improve COGM accuracy?
A: AI systems like SAP's S/4HANA achieve 97.3% COGM accuracy by automatically classifying expenses and predicting waste. They flag anomalies, like a 15% glue cost increase in cabinet production, before it impacts margins. Source 1's study shows these tools reduce calculation time by 68%.
Q: Should overtime pay be included in COGM?
A: Yes, both regular and overtime wages for production staff count as direct labor costs. However, administrative overtime belongs in overhead. A furniture maker would include extra pay for assembly line workers during holiday rushes, but not for accounting staff working late.
M production costs. Source 3 shows how a toolmaker won contracts by lowering COGM 8% through waste reduction. Track labor efficiency and material waste percentages monthly to find savings.
Q: What's the biggest mistake in COGM calculations?
A: Forgetting work-in-progress (WIP) adjustments causes 42% of errors, as Source 1 found. If you have ,000 materials + ,000 labor but ,000 unfinished goods, your COGM isn't ,000. You must subtract the ,000 WIP. Always count partially completed items separately.
Q: How do AI tools improve COGM accuracy?
A: AI systems like SAP's S/4HANA achieve 97.3% COGM accuracy by automatically classifying expenses and predicting waste. They flag anomalies, like a 15% glue cost increase in cabinet production, before it impacts margins. Source 1's study shows these tools reduce calculation time by 68%.
Q: Should overtime pay be included in COGM?
A: Yes, both regular and overtime wages for production staff count as direct labor costs. However, administrative overtime belongs in overhead. A furniture maker would include extra pay for assembly line workers during holiday rushes, but not for accounting staff working late.